Usage detail
Golf ball covers, molded products, films, extrusion coating, automotive moldings, modifiers, etc.
- Overview
- Grade Chart
- Physical properties
- Usage detail
- Product Safety Information
Introduction
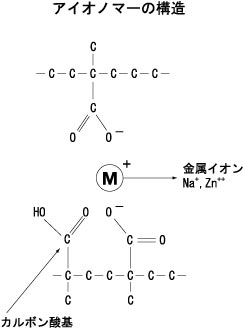
HIMILAN™ is an ionomer resin manufactured by Dow-Mitsui Polychemicals using technologies from the Dow Chemical Company.
Dow Chemical (DuPont at the time of development) developed the ionomer resin SURLYN™, an ethylene-methacrylic acid copolymer cross-linked with metal ions between its molecules, and supplies it to countries around the world.
Dow-Mitsui Polychemicals was also importing and selling SURLYN™ in Japan, but due to expanding domestic demand, from autumn 1978 the company began manufacturing ionomer resin using the same method as the US-based DuPont (as it was then known), and marketed it under the product name HIMILAN™.
* SURLYN™ is denotes a trademark of the Dow Chemical Company or its affiliates.
Features
- Is extremely tough, with moderate elasticity and flexibility.
- Has excellent cold resistance.
- Features outstanding wear resistance.
- Has good transparency.
- Has stable thermal adhesion to metals, etc. because it has carboxylic acid groups.
- Exhibits excellent oil resistance.
- Has outstanding stress crack resistance.
- Has excellent compatibility with pigments and fillers.
- Is capable of plastic molding similar to polyethylene.
HIMILAN™ has side chains of carboxylic acid groups in its polyethylene molecular chain, and some of these carboxylic acid groups form a structure of cross-linking between molecular chains by way of metal cations. Many superior properties are created due to these two structural characteristics. Particularly the cross-linking through metal ions differs from general cross-linking through chemical bonds. Specifically, the bonding strength changes with heat, with heating weakening the bonding strength, and cooling strengthening it.
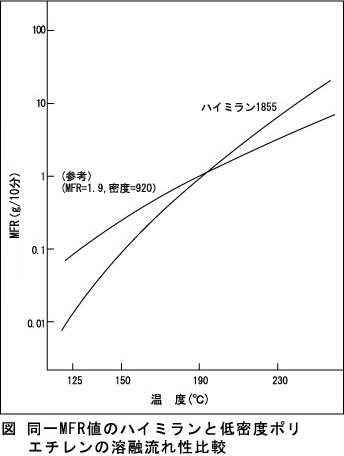
For example, this figure shows the relationship between temperature and flow properties. As ion crosslinking is weakened by heat, it can be molded in the same way as a regular thermoplastic resin, and due to the existence of cross-links, even when melted it is superior to low density polyethylene in terms of melt strength and melt stretch properties. As ion bonding is further strengthened in its hardened state, its toughness increases.
Table: Comparison of the physical properties of HIMILAN™ and other materials
Property | Test method ASTM |
HIMILAN™ | Reference | ||||
Low density polyethylene (LDPE) |
Rigid PVC |
Polypropylene | Polycarbonate | Nylon | |||
Specific gravity g/㎥ |
D-792-60T | 0.93 - 0.97 | 0.91 - 0.93 | 1.32 - 1.45 | 0.90 - 0.91 | 1.20 | 1.13 - 1.16 |
---|---|---|---|---|---|---|---|
Mechanical properties | |||||||
Break point Tensile strength MPa |
D-412-51T | 20 - 35 | 6.9 - 16 | 34 - 62 | 24 - 39 | 55 - 66 | 39 - 64 |
Elongation % |
D-412-51T | 300 - 500 | 100 - 650 | 2 - 40 | 250 - 700 | 60 - 100 | 25 - 300 |
Izod impact strength (notched) J/m |
D-256 | >830 | >830 | 4.9 - 80 | 31 - 110 | 640 - 850 | 53 - 200 |
Elmendorf tearing N/cm |
- | 78 - 300 | 240 - 780 | 39 - 2700 | 20 - 5900 | - | - |
Bending rigidity MPa |
D-790 | 70 - 370 | 120 - 250 | 2500 - 2800 | 1000 - 1400 | - | 520 - 2500 |
Surface hardness RockWell Shore |
- D-785 |
- D56 - 68 |
R25 - 35 D41 - 46 |
R104 - 115 A70 - 90 |
R85 - 110 - |
M78 - |
R103 - 118 - |
Thermal properties | |||||||
VICAT softening point ℃ |
D-1525 | 57 - 80 | 85 - 97 | 80 - 100 | 140 - 150 | 150 | - |
Loaded heat deformation temperature ℃(at0.45MPa) |
D-648 | 43 - 49 | 41 - 51 | 54 - 78 | 100 - 110 | 143 | 127 - 170 |
Coefficient of expansion cm/cm/℃✕105 |
D-696 | 11 - 13 | 16 - 18 | 7.2 - 7.8 | 10 - 15 | 3.7 - 7.0 | - |
Brittle temperature ℃ |
D-746 | -50 - -112 | <-76 | -29 | -23 | <-100 | -57 |
Electrical properties | |||||||
Volume resistivity Ωcm |
D-257 | E+16 - E+18 | E+17 | E+15 | >E+16 | E+17 | E+12 - E+15 |
Dielectric constant (60Hz) |
D-150 | 2.3 - 2.5 | 2.3 | 3.4 | 2.3 | 3.17 | 4.9 - 10.0 |
Power factor (103Hz) |
D-150 | 0.001 - 0.004 | <0.0005 | 0.02 | 0.0008 | 0.0009 | 0.06 - 0.11 |
Withstand voltage kV/mm |
D-149 | 35 - 43 | 21 - 35 | 48 | 21 - 29 | 17 | 19 - 24 |
Transparency | |||||||
Steam (0.1mm·g/m2·day) (35℃,95%RH) |
- | 4 - 8 | 4 - 6 | 16 | 0.24 - 2.8 | 13 - 15 | 30 |
Oxygen 10-16mol·m/m2·S·Pa |
D-1434 | 6.0 - 10 | 4.0 - 8.0 | 0.3 | 12 | 0.2 - 3.0 | 0.5 |
Carbon dioxide 10-16mol·m/m2·S·Pa |
D-1434 | 20 - 40 | 40 | 1.0 | - | - | 3.2 |
Nitrogen gas 10-16mol·m/m2·S·Pa |
D-1434 | 1.3 - 3.4 | 2.0 - 4.0 | - | - | - | - |
Chemical resistance | |||||||
Weak acid | D-543 | sA | R | R | R | R | R |
Strong acid | D-543 | sA | sA | R | sA | sA | A |
Weak alkaline | D-543 | R | R | R | R | R | R |
Strong alkaline | D-543 | R | R | R | R | A | R |
Hydrocarbon solvent | D-543 | S | S | S | sS | sA | R |
Ketone alcohol | D-543 | sS | R | D | R | R | R |
← Swipe →
R: withstands, S: swells, A: affected, sS: swells slightly, sA: affected slightly, D: melts
Note: The displayed data are typical values and cannot be used as standard values.
Grade Chart
Comparison of the physical properties of HIMILAN™ and other materials
Grade | Ion type | Item | Measurement method |
Density | Tensile stress at break |
Tensile breaking strain |
Bending rigidity |
Durometer D hardness |
Vicat softening temperature |
Melting point |
Brittle temperature |
Optical properties (1 mm thickness) *2 | Food hygiene ○: Listed (acquired), ✕: Not listed (not acquired) - : Unknown 1) Dow-Mitsui Polychemicals has not conducted an elution test using a food simulant-solvent. 2) Even if it is listed (acquired), there may be various restrictions and other requirements, please make sure to confirm the details with us. 3) Food hygiene information does not necessarily reflect the latest version of each law or regulation (including voluntary standards). Please be sure to confirm the details with us. |
||||
---|---|---|---|---|---|---|---|---|---|---|---|---|---|---|---|---|---|
Haze | Total light transmittance | ||||||||||||||||
Measurement method |
JIS K7210 :1999 (190℃, 2.16㎏ load) |
JIS K7112 :1999 |
JIS K7161-1:2014 K7161-2:2014*1 |
JIS K7161-1:2014 K7161-2:2014*1 |
JIS K7106 :1995 |
JIS K7215 :1986*3 |
JIS K7206 :1999 |
(DSC) | JIS K 7216 :1980 |
JIS K7136 :2000 |
JIS K7361-1 :1997 |
||||||
Unit | g/10min | ㎏/m3 | MPa | % | MPa | - | ℃ | ℃ | ℃ | % | % | MHLW Positive Lists |
JCII Center JHOSPA Type Confirmation Certificate |
US FDA 21CFR |
European PIM |
||
1706 | Zn | 0.9 | 960 | 33 | 300 | 310 | 68 | 65 | 88 | -60 以下 | 2.6 | 92 | 〇 | 〇 | 〇 | 〇 | |
1705 | Zn | 5.0 | 950 | 31 | 400 | 200 | 63 | 65 | 91 | -60 以下 | 5.6 | 91 | 〇 | 〇 | 〇 | 〇 | |
1702 | Zn | 16 | 950 | 27 | 400 | 170 | 62 | 63 | 90 | -60 以下 | 7.4 | 91 | 〇 | 〇 | 〇 | 〇 | |
1650 | Zn | 1.5 | 950 | 30 | 400 | 250 | 63 | 74 | 96 | -60 以下 | 7.8 | 87 | 〇 | 〇 | 〇 | 〇 | |
1557 | Zn | 5.5 | 950 | 24 | 400 | 260 | 63 | 72 | 95 | -60 以下 | 16 | 88 | 〇 | 〇 | 〇 | 〇 | |
1554W | Zn | 1.0 | 960 | 32 | 400 | 270 | 65 | 71 | 95 | -60 以下 | 10 | 88 | 〇 | 〇 | 〇 | 〇 | |
1652 | Zn | 5.5 | 940 | 24 | 500 | 160 | 58 | 80 | 98 | -60 以下 | 27 | 84 | 〇 | 〇 | 〇 | 〇 | |
AM7326 | Zn | 1.1 | 950 | 30 | 400 | 280 | 62 | 83 | 101 | -60 以下 | 17 | 85 | 〇 | 〇 | 〇 | 〇 | |
1855 | Zn | 1.0 | 960 | 32 | 400 | 92 | 60 | 56 | 86 | -60 以下 | 5.7 | 91 | 〇 | 〇 | 〇 | 〇 | |
1707 | Na | 0.9 | 940 | 33 | 300 | 310 | 67 | 60 | 89 | -60 以下 | 3.5 | 92 | 〇 | 〇 | 〇 | 〇 | |
1605 | Na | 2.8 | 940 | 35 | 400 | 320 | 68 | 66 | 92 | -60 以下 | 3.3 | 92 | 〇 | 〇 | 〇 | 〇 | |
1555 | Na | 10 | 940 | 23 | 400 | 240 | 63 | 72 | 95 | -60 以下 | 15 | 90 | 〇 | 〇 | 〇 | 〇 | |
1601 | Na | 1.3 | 940 | 31 | 400 | 230 | 63 | 73 | 97 | -60 以下 | 6.8 | 91 | 〇 | 〇 | 〇 | 〇 | |
AM79021 | Na | 2.8 | 940 | 29 | 400 | 250 | 63 | 75 | 97 | -60 以下 | 10 | 88 | 〇 | 〇 | 〇 | 〇 | |
LDPE | 0.9 | 920 | 17 | 600 | 170 | 48 | 93 | 109 | -60 以下 | 96 | 78 | ||||||
EVA | (VA10%) | 9.0 | 930 | 15 | 700 | 72 | 41 | 71 | 96 | -60 以下 | 89 | 85 |
← Swipe →
* 1 Tensile test - test piece type and testing speed: JIS K 7161-2 / 1BA / 20
* 2 Conditions for creating a test piece for optical properties (JIS K7151, cooling method: B method)
* 3 Measurement instrument: Asker P-2 sensor descent rate: 10.0 mm / s
· Note: The data above are typical values and cannot be used as standard values.
· As there are large differences between different grades of HIMILAN, please consult with Dow-Mitsui Polychemicals when deciding on which grade to use.
· Only typical grades are listed in this table. Please contact Dow-Mitsui Polychemicals to inquire whether there are any grades other than those listed.
Physical properties
Usage detail
Product Safety Information
1. Medical applications
Please do not use this product for permanent implantation in the human body or for medical applications involving a state of permanent contact with bodily fluids or human tissue (in this case, permanent means 30 days or more.)
Additionally, please consult with Dow-Mitsui Polychemicals in advance if you wish to use the product for other medical applications, such as for a medical device as defined in the Act on Securing Quality, Efficacy and Safety of Products Including Pharmaceuticals and Medical Devices.
2. Food packaging applications
Please contact Dow-Mitsui Polychemicals regarding the state of inclusion in (conformity to) domestic and overseas laws or regulations regarding food utensils, containers and packaging materials.
Outside of Japan, some grades of Himilan® ionomer resin are available as ‘Surlyn™’ from the Dow Chemical Company.
Heat sealing properties
The greatest feature of HIMILAN™ is that it has outstanding heat sealing functions in practical use.
In particular, the hot tack properties of HIMILAN™ are at the highest level for a heat sealing material. For example, it has several times the hot tack strength of low density polyethylene, and that outstanding hot tack strength is produced across a wide range of heat sealing temperatures from low to high.
In addition, HIMILAN™ is superior to low density polyethylene by several orders of magnitude in every respect, including low temperature heat sealing and foreign matter adhesion sealing properties. This makes HIMILAN™ a heat sealing resin that boasts a wide range of heat sealing temperature conditions.
The superior heat sealing properties of HIMILAN™ improve the packaging speed of high-speed bag filling and packing machines, reduce sealing loss, and help improve the reliability of packaging with vacuum packaging and gas flush packaging.
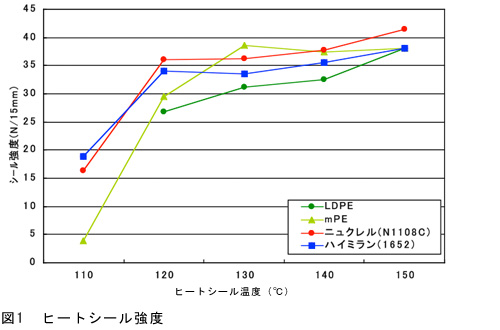
- Measurement method
-
- Composition: PET (12 µm) / LDPE(15 µm) / Evaluated resin (30 µm)
* LDPE:MFR=7.2,d=917、mPE:MFR=7,d=912 - Processing resin temperature: LDPE / mPE / NUCREL*: 295ºC, HIMILAN™ 300ºC
- Heat sealing conditions: 0.2 MPa x 0.5 sec., sealing bar width: 10 mm
- Heat sealing strength measurement conditions: Peel rate: 300 mm / min., peel angle: 90º (T type), test specimen width: 15 mm
- Composition: PET (12 µm) / LDPE(15 µm) / Evaluated resin (30 µm)
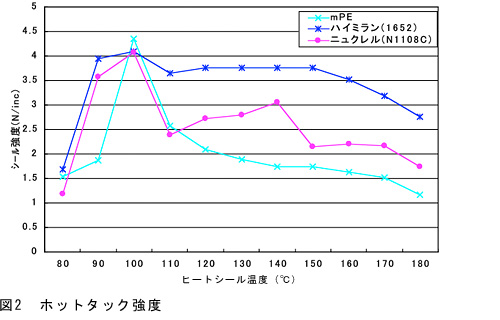
- Source: Dow-Mitsui Polychemicals technical materials
-
- Equipment: Tella Model HT hot tack heat sealing tester
- Composition: paper (50 g/m²) / LDPE (20 µm) / AL foil (7 µm) / AC + ozone evaluated resin (20 µm)
* mPE: MFR=8, d=901, HIMILAN™ / NUCREL* are AC + no ozone treatment - Processing resin temperature: mPE / NUCREL*: 295ºC, HIMILAN™: 310ºC
- Hot tack strength: measured 185ms after heat sealing
Bond characteristics
Grade Selection Guidelines
HIMILAN™ can achieve hot melt adhesion to materials such as metals and nylon because it has carboxylic acid groups.
For example, HIMILAN™ exhibits good adhesive strength to aluminum foil without a primer (extrusion coating method). It can also be bonded to nylon using a co-extrusion technique.
Table: Adhesion to aluminum foil using the extrusion coating method(No anchor coating)
Laminate temperature | |||||||
---|---|---|---|---|---|---|---|
315℃ | 280℃ | ||||||
Laminate thickness(µm) | 15 | 20 | 30 | 40 | 20 | 40 | |
Adhesive strength | HIMILAN™ 1652 | 2.5 | 3.4 | 4.4 | 5.4 | 2.5 | 4.4 |
(Reference) LDPE | - | 1.5 | - | 3.4 | 0 | 0 |
Unit: N/15 mm
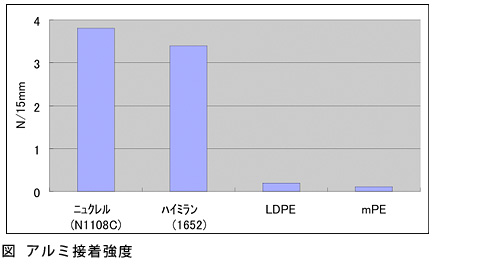
- Measurement method
-
- Composition: paper (50 g/m2) / LDPE (20 µm) / Al (9 µm) / evaluated resin (20 µm)
* LDPE: MFR=8, d=917, mPE: MFR=11, d=906 - Processing resin temperature: NUCREL* / LDPE: 290ºC, HIMILAN™ 293ºC, mPE: 287ºC
- Aging conditions: 23ºC x 50% RH
- Adhesion strength measurement: Peel rate: 300 mm / min., peel angle: 90° (T type), test specimen width: 15 mm
- Composition: paper (50 g/m2) / LDPE (20 µm) / Al (9 µm) / evaluated resin (20 µm)
Molding and Automotive Applications
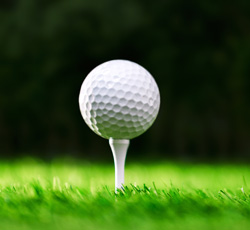
Golf balls
Due to its moderate elasticity and excellent cut resistance, HIMILAN™ is used in golf balls (cover) as a substitute for conventionally used rubber.
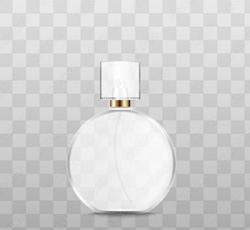
Injection molded goods: decorative caps
Utilizing its good gloss and transparency combined with excellent crimp transferability, HIMILAN™ is used for cosmetics containers and similar items.
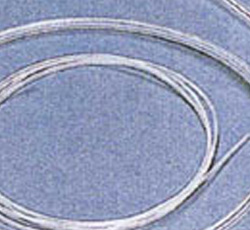
Hoses and Tubes
Thanks to its excellent stress crack resistance combined with flexibility, transparency and good scratch resistance, HIMILAN™ is used in hoses, tubes and covering materials.
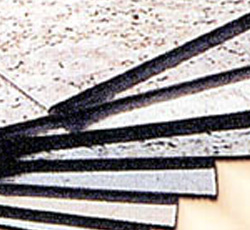
Building materials and shoe counters
As HIMILAN™ does not scratch easily and features excellent wear and flex resistance, it is used in building materials and shoe counters.
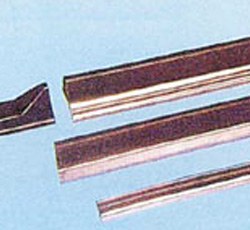
Automotive exterior components
As HIMILAN™ has excellent scratch, impact and wear resistance, it is used for automotive exterior components.
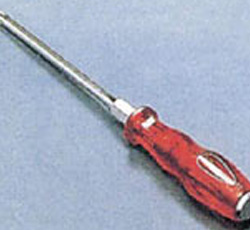
Screwdrivers
As HIMILAN™ is impact resistant and exhibits excellent wear and scratch resistance, it is used in the grips of screwdrivers and similar tools.
Extrusion Coating Applications
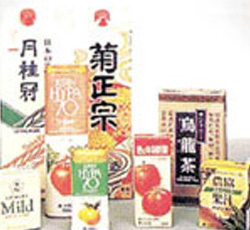
Paper-based liquid containers
Due to its excellent adhesiveness to metal, wood and paper, combined with high speed processing capabilities, HIMILAN™ is used for paper containers (aluminum foil composition) to hold alcohol, juice and other beverages.
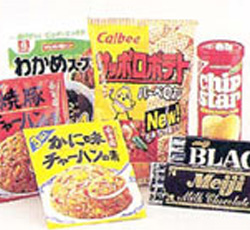
Snack and powder packaging
When laminated to a film, HIMILAN™ reduces pinholes caused by flexing or the contents breaking through, and improves sealing in gas barrier packaging and the like.
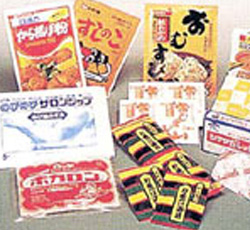
Pharmaceutical and powder packaging
As HIMILAN™ supports a wide range of heat sealing conditions and features excellent low temperature sealing and hot tack properties, it improves the productivity of automated filling and packaging and can reduce sealing loss.
Film Applications
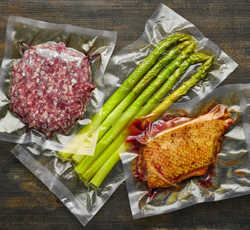
Meat packaging
As the thickness remains uniform even when the film is heavily squeezed and a wide range of squeezing conditions are supported, HIMILAN™ is used in packaging materials for blocks of meat, ham, bacon and so on.
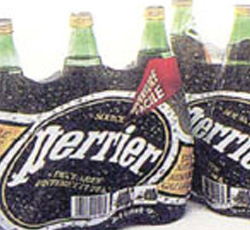
Various packaging
Films manufactured using inflation or casting methods can be easily and linearly torn in the transverse direction (TD).
Modification, Coating and Adhesive Applications
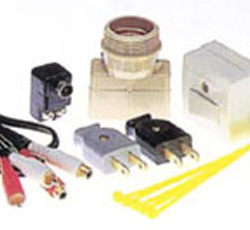
Resin modifiers
HIMILAN™ is highly compatible with various engineering plastics and polyolefins, and is used as a modifier to improve the impact resistance of nylon or the workability of polyester, among other applications.
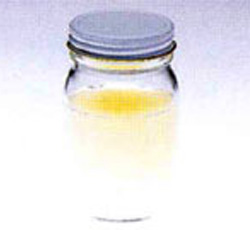
Water-based coatings and adhesives
HIMILAN™ and NUCREL* can be dispersed in water with caustic soda, ammonia and other substances, and can be used as a raw material for water-based coatings, adhesives and so on.